Steel structures form the backbone of modern infrastructure, ranging from transmission towers to bridges and industrial frameworks.
While steel is valued for its strength and durability, the continuous monitoring and maintenance of these structures are vital to ensure their long-term integrity.
This is where Structural Health Monitoring (SHM) comes into play, providing essential data to track the condition of steel structures over time.
What is Structural Health Monitoring
Structural Health Monitoring (SHM) is the systematic, ongoing assessment of a structure's condition, utilizing accurate, real-time measurements from sensors and advanced technologies.
These smart sensors monitor critical parameters such as stress, strain, vibration, inclination, and external environmental factors, including temperature and humidity.
The collected data is transmitted to a central control system, which analyzes it for irregular patterns and generates alerts if any anomalies are detected.
In the context of steel structures like transmission towers, SHM systems play a crucial role in identifying early signs of damage or wear, enabling timely maintenance and repairs.
By facilitating proactive interventions, SHM is essential for extending the lifespan of critical infrastructure and enhancing overall safety.
Key Components of SHM in Steel Structures
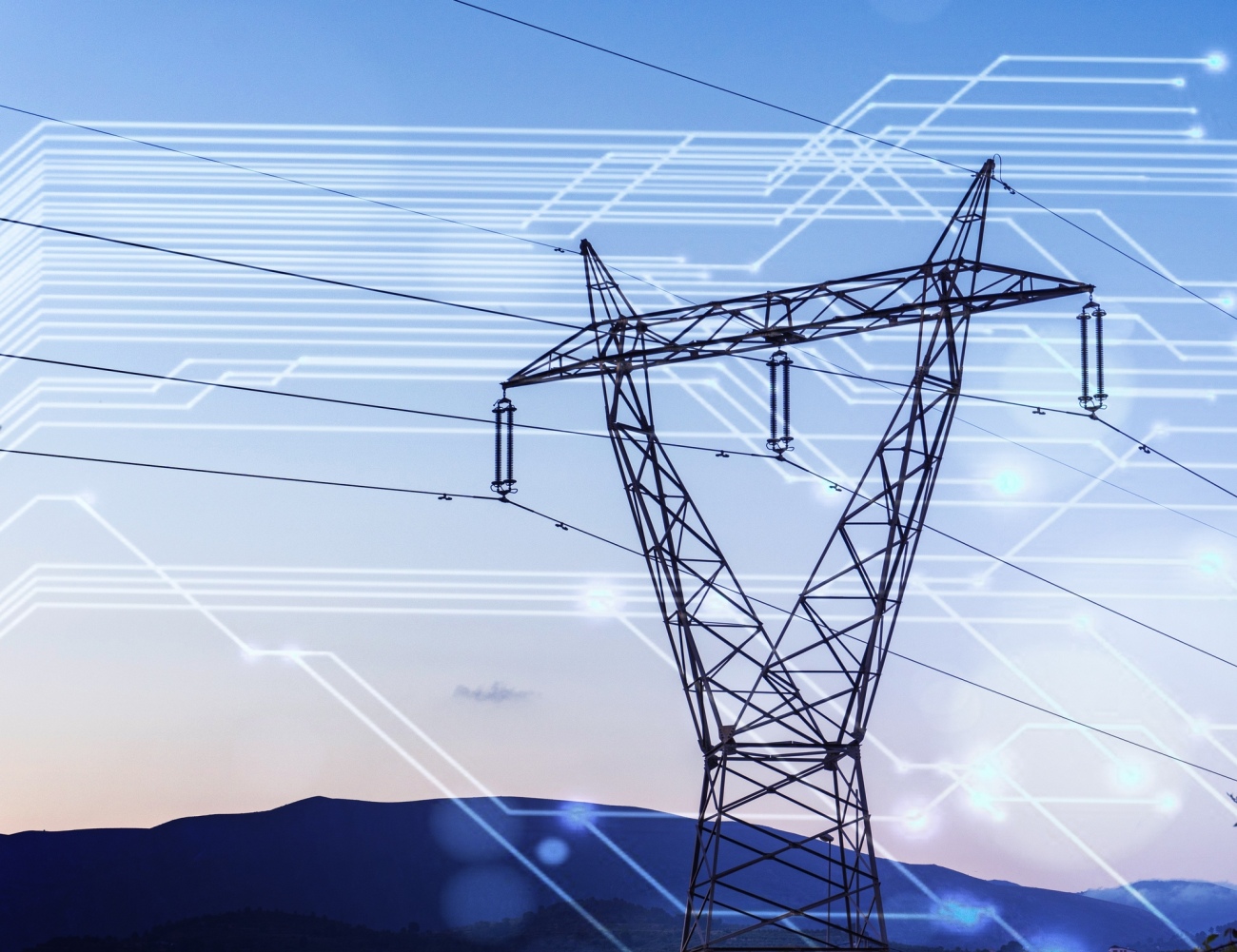
Sensors and Instrumentation
Strain Gauges
Strain gauges are used to monitor deformation in steel components under operational loads.
When subjected to force, the sensing foil is deformed, leading to a change in its electrical resistance.
This change can be precisely measured, providing critical data on load distribution and helping engineers identify potential failure points within the structure.
Accelerometers
Accelerometers are electromechanical devices that measure acceleration forces in one or multiple axes, capturing both static forces, such as gravity, and dynamic forces from vibrations.
In SHM, they provide real-time data on changes in dynamic characteristics, enabling the detection of damage or altered performance.
Multi-axis accelerometers are crucial for assessing dynamic loads from various sources, such as traffic, construction, and seismic events.
Temperature Sensors
Temperature sensors are essential for monitoring thermal variations in civil engineering structures, as temperature changes can significantly impact their physical properties.
Thermocouples, commonly used in large concrete structures, measure temperature at specific points to ensure proper control during curing and construction.
By providing real-time data on thermal expansion and contraction, these sensors enable engineers to anticipate and address thermal stress-related issues in steel structures.
Fiber Optic Sensors
Fiber optic sensors utilize light transmission to monitor parameters such as strain, temperature, and pressure in civil engineering structures.
Their versatility allows for both local monitoring—focusing on material behavior—and global assessments of overall structural performance.
These sensors have proven effective in applications such as strain monitoring in bridge components and are particularly beneficial for structural health monitoring due to their compact size, lightweight nature, and immunity to electromagnetic interference.
Advanced types, such as Fiber Bragg Grating (FBG) and Distributed Fiber Optic Sensors (DFOS), are particularly effective for detecting and monitoring corrosion, providing real-time insights into material degradation.
FBG sensors utilize periodic refractive index variations to measure parameters and are commonly used to assess the integrity of reinforcing bars and steel structures, while DFOS can continuously monitor corrosion across larger spatial scales, enhancing the understanding of the interaction between structural loads and corrosion effects.
Inclinometers and Tiltmeters
Inclinometers are precision instruments that monitor horizontal subsurface movements and deformations, providing real-time data on stability when installed in boreholes or attached to structures.
Similarly, tiltmeters detect minute changes in inclination, measuring angles of slope or elevation with respect to gravity.
Together, these devices offer critical insights into structural integrity, helping to ensure that movements remain within design limits and facilitating early warnings of potential structural damage.
Drone Technology for Inspections
The integration of drone technology with SHM systems enhances inspection capabilities for steel structures.
Drones equipped with sensors and cameras can conduct remote inspections, gathering detailed visual data from hard-to-reach areas. By combining drone-based inspections with SHM, engineers can efficiently verify the condition of steel structures, identify surface-level issues like corrosion or cracks, and cross-check this data against SHM sensor readings.
This holistic approach enables more accurate assessments and minimizes the need for costly manual inspections.
Data Collection and Analysis
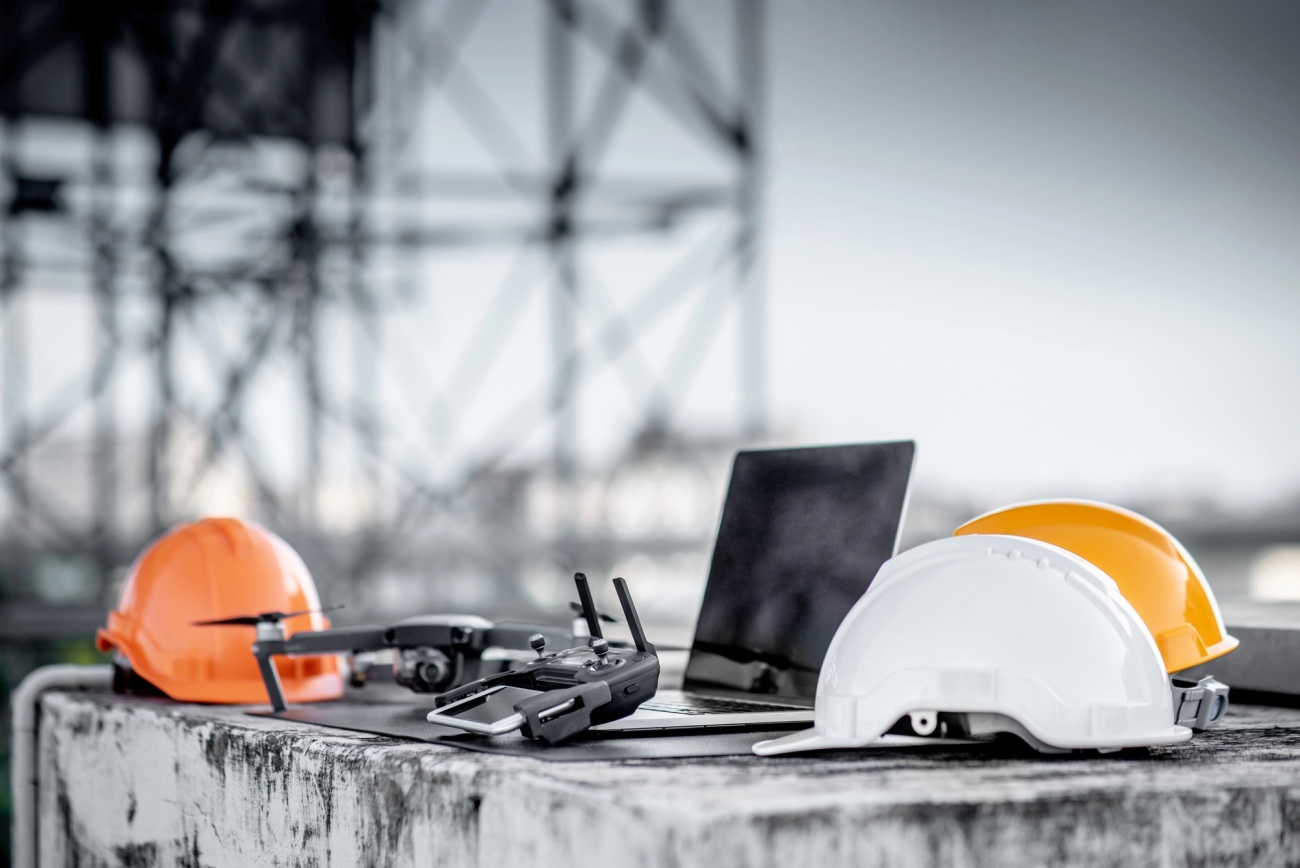
SHM systems generate vast amounts of data that can be analyzed to assess a structure’s current condition and predict future performance.
By combining data from different sensors, engineers can identify patterns indicating structural fatigue, corrosion, material degradation, changes in load-bearing capacity, or other potential risks that may affect the integrity and safety of the structure.
Integrating AI into SHM systems enhances data processing, enabling machine learning algorithms to detect subtle signs of structural deterioration that human operators might overlook. This capability allows for more accurate predictions and faster response times, facilitating timely interventions before significant problems arise.
Alert and Response Systems
Modern SHM solutions include real-time alert mechanisms that notify engineers of potential risks.
Early detection of structural weaknesses enables targeted inspections and interventions, preventing costly failures and ensuring the continued safety and functionality of steel structures.
Benefits of SHM for Steel Structures
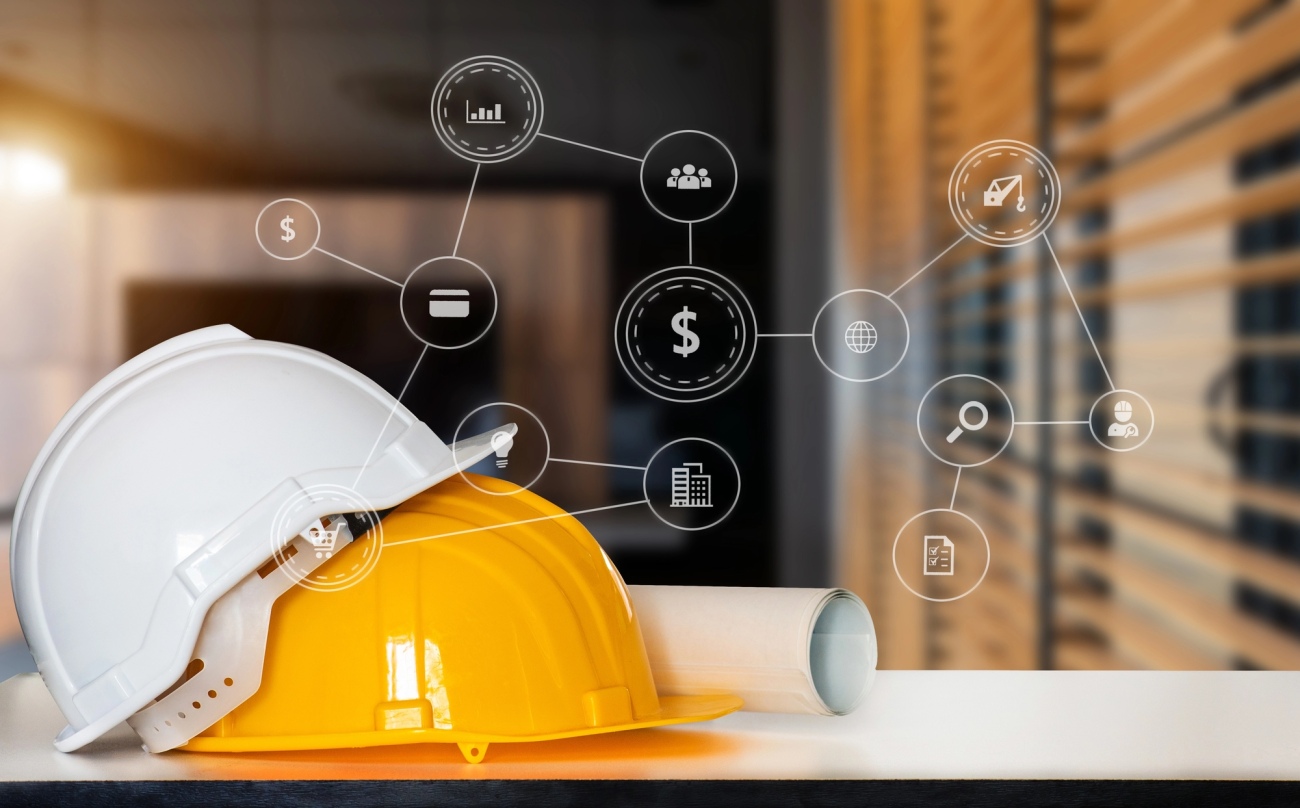
Proactive Maintenance
SHM allows for data-driven maintenance, scheduling repairs based on actual structural conditions rather than arbitrary timelines.
This reduces costs by minimizing unnecessary interventions and preventing small issues from escalating.
The incorporation of AI further optimizes this process by enabling predictive maintenance, addressing potential issues before they develop into costly or dangerous failures.
Enhanced Safety
By providing early warnings of potential structural weaknesses, SHM improves the safety of steel structures, especially those in high-risk environments such as energy infrastructure.
Sustainability and Resource Optimization
In alignment with the principles of sustainability, SHM contributes to a more responsible use of steel by extending the lifespan of structures and minimizing unnecessary replacements.
By using real-time data to optimize maintenance schedules, SHM reduces material waste and promotes more efficient resource use, thereby supporting a circular economy where maintenance and reuse are prioritized over new construction.
This approach not only lowers the environmental footprint but also aligns with the broader goals of sustainability in the infrastructure sector.
Optimized Design
Data from SHM systems can feed into future designs, improving resilience by identifying stress points and failure-prone areas in existing steel structures.
This information is crucial for retrofitting transmission towers, allowing targeted enhancements that ensure structural integrity and extend service life.
Innovative Sensor Technologies: The Simplicity of Colour-Changing Materials
An exciting development in SHM technology comes from Assistant Professor Mohammad Fotouhi at TU Delft, who has been developing cost-effective colour-changing sensor materials.
Inspired by the natural ability of opals and chameleons to change colour in response to external stimuli, Fotouhi’s material changes colour to indicate critical damage or remaining lifespan in structures.
This technology simplifies structural monitoring by eliminating the need for complex, energy-intensive sensor systems.
When a structure is under high mechanical stress, the sensor material visibly changes colour, offering a clear, low-cost way to detect early signs of structural issues.
As highlighted in his research, this innovation could be a game-changer for industries where cost-effective, sustainable monitoring solutions are in high demand.
This aligns with the broader goal of using smart and sustainable techniques for SHM, providing a solution that is not only simple but also scalable across various sectors, from aviation to construction.
By using materials that integrate the sensor function directly, industries can reduce the cost and complexity of SHM while improving long-term reliability.
Conclusion
Structural Health Monitoring is a crucial element in the maintenance and optimization of steel structures.
By combining real-time data collection, AI-driven analysis, and advanced inspection technologies like drones, SHM systems provide invaluable insights that enhance the safety, efficiency, and sustainability of infrastructure.
As steel structures face increasing demands from environmental conditions and operational loads, SHM systems will play an even greater role in ensuring their long-term resilience —a critical focus of the EU Grid Action Plan.
The integration of AI, sustainability practices, and innovative sensor materials makes SHM a key contributor to a future where steel structures are not only robust but also resource-efficient and eco-friendly.